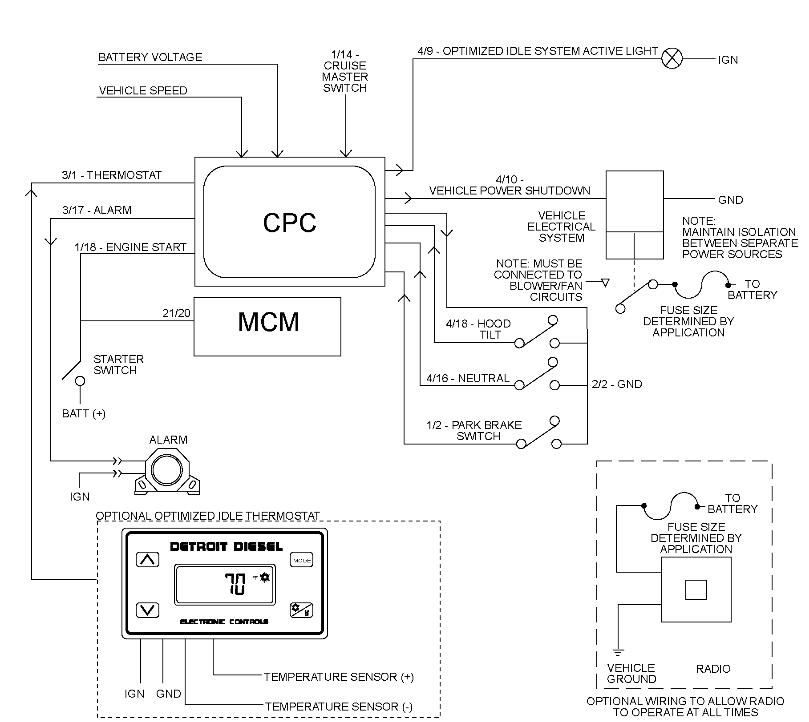
This instruction show you guide on how to solve/optimize idle will arm but will not restart the engine for Detroit EPA07 GHG14 DDEC VI 10.
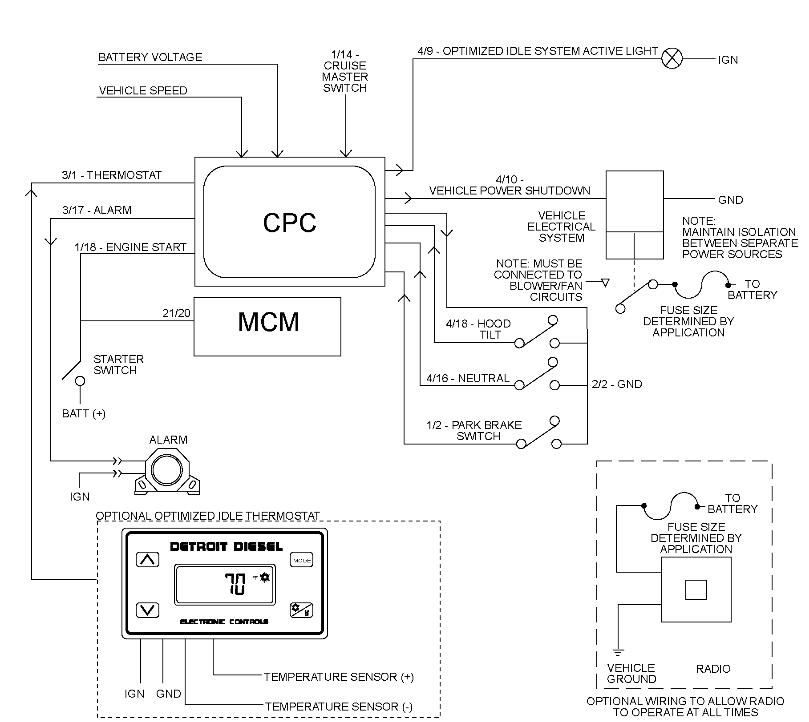
Preparations:
DDDL 8.18 2023
Nexiq USB Link 2 Adapter
Procedures:
Check as follows:
1 Is MCM fault code SPN 1663 /FMI 7 present?
1aYes; troubleshoot this code first.
1b No; Go to step 2.
2 Was the CPC recently programmed?
2a Yes; check for proper CPC parameter settings. Refer to section “Optimized Idle” of the A&I Manual (See table below).
2b No; Go to step 3.
3 Using DiagnosticLink, verify the operation of the Optimized Idle Safety Loop and the Vehicle Speed Sensor (VSS). Under Instrumentation, go to the Chart tab and select the following on the chart:
- DSL: Parking Brake
- DSL: Hood Tilt Switch
- DSL: Neutral Switch
- ASL: Road Speed
Cycle each switch and monitor their functionality. Monitor the Road Speed; it should read zero when the vehicle is stationary.
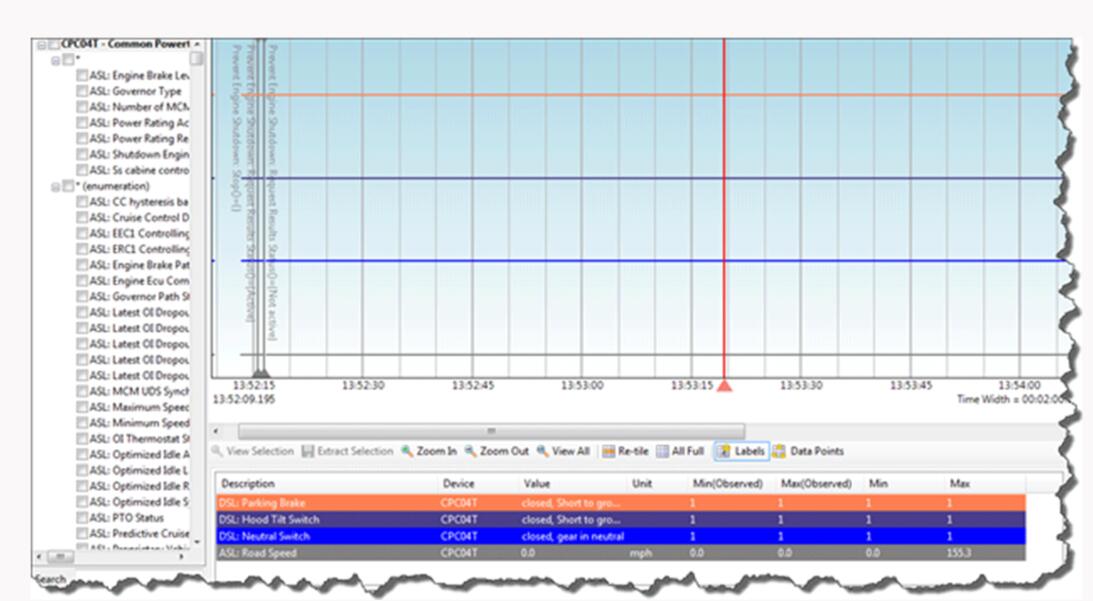
Was a fault with either the Optimized Idle Safety Loop or VSS found?
3a Yes; repair as necessary.
3b No; Go to step 4.
4 Is the vehicle equipped with an Auxiliary Power Unit (APU) or ParkSmart?
4a Yes; vehicles with an APU or ParkSmart may not use Optimized Idle to control the cab temperatures. If this is the customer’s complaint, refer to the APU or ParkSmart operation instructions.
4b No; Go to step 5.
5 Check the Optimized Idle Thermostat settings; Refer to section “Thermostat Operation” of the Optimized Idle User Manual (DDC-SVC-MAN-0019) . Is the Optimized Idle Thermostat properly configured?
5a Yes; install a test CPC. Go to step 6.
5b No; Refer to section “Thermostat Operation” of the Optimized Idle User Manual (DDC-SVC-MAN-0019) . Verify repair.
6 Will Optimized Idle work correctly with the test CPC?
6a Yes; replace the CPC.
6b No; Go to step 7.
7 Set the Optimized Idle Thermostat mode to cool the cab and put the vehicle on Optimized Idle mode. Using a heat gun, apply heat to the Optimized Idle Thermostat Skin Temperature sensor; refer to OEM literature for sensor location. Did Optimized Idle start the engine to cool the cab?
7a Yes; Refer to section “Optimized Idle” of the A&I Manual (See table below) for proper Optimized Idle parameter configuration
7b No; Go to step 8.
8.Monitor the Optimized Idle Thermostat temperature reading while applying heat to the sensor. Is the reading on the Thermostat display accurate?
8a Yes; replace the Optimized Idle Thermostat.
8b No; Go to step 9.
9 Disconnect the Optimized Idle Thermostat electrical connector and measure the resistance between pin 3 of the Optimized Idle Thermostat connector, harness side and the sensor ground circuit of the Skin Temperature sensor harness side connector. Is the resistance less than five ohms?

9a Yes; Go to step 10.
9b No; repair the circuit.
10 Measure the resistance between pin 1 of the Optimized Idle Thermostat connector, harness side and the sensor signal circuit of the Skin Temperature sensor harness side connector. Is the resistance less than five ohms?
10a Yes; replace the Optimized Idle Thermostat.
10b No; repair the circuit.