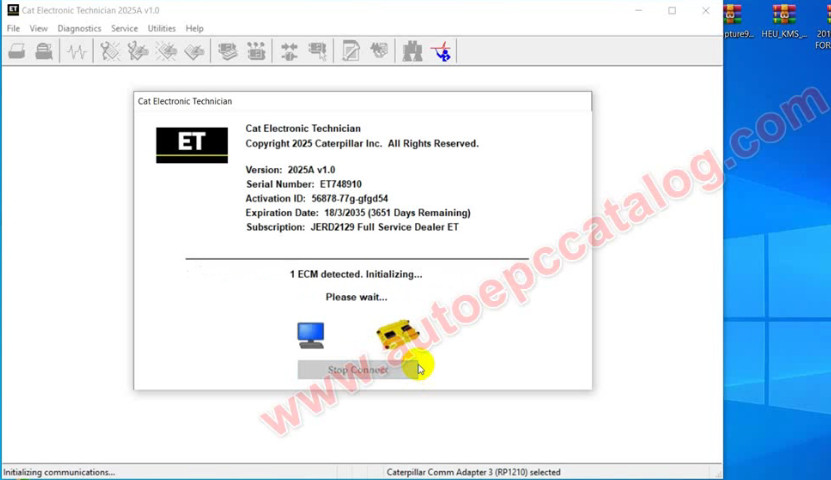
CAT ET 2025A Diagnostic software System Troubleshooting Settings function allows the troubleshooting parameters “Value” and “Mode” to be viewed and changed. This function puts parameters in and out of override mode.
The parameters that are changed to override mode stay in this mode until they are disabled in the System Troubleshooting Settings screen or the ECM is turned off. Turning off the ECM resets the ECM parameters back to their normal settings.
Related Contents:
Accessing
To run the System Troubleshooting Settings function, select “Diagnostic Tests” from the Diagnostics menu on CAT ET 2025A, and then select “System Troubleshooting Settings” from the submenu. The System Troubleshooting Settings screen is displayed.
Screen Layout
The System Troubleshooting Settings screen has the following areas:
Display Area
The System Troubleshooting Settings display area has four columns:
Description – Provides the name of the parameter
Value – Displays the status of the current parameter
Unit- Displays the unit of measure for the value
Mode – Displays the mode of the parameter: “Normal” or “Override”
Buttons
The buttons available in the System Troubleshooting Settings screen are:
Disable Override – Click this button to take the selected parameter out of override mode.
Note: When an unavailable parameter (read only) is selected, the Change button is disabled.